SERVICES
Advance Materials Consultancy
P91 and 92 Inspection, Quality Checks, Integrity/ Life Assessment
Challenges
Some of the biggest challenges facing P91 users worldwide are:
- Minimizing the risk of premature failure of P91 welded components operating under creep conditions due to accumulation of damage in the fine-grained region – or Type IV position – of the heat-affected zone (HAZ).
- Dealing with P91 components/welds with abnormal or aberrant (i.e. non-martensitic) microstructures and sub-standard rupture strength.
- Thermal fatigue or creep-fatigue cracking in thick-section components.
- Steam-side oxidation leads to overheating and premature rupture of thin-walled tubes.
AMCO Integrity Pty Ltd with its Technical Partner in the UK has unrivaled knowledge and experience of the potential issues. The company has developed and offers an arsenal of techniques for inspection, monitoring, and life assessment that can help P91 users to maintain the safe and reliable operation of their plant.
Non-Destructive Examination/Inspection and Life/Condition Assessment
- AMCO Integrity Pty Ltd’s site services team provides a comprehensive range of inspection techniques for detection and monitoring of creep damage and other forms of degradation or cracking. As well as conventional NDE techniques, AMCO Integrity Pty Ltd uses ToFD and Phased Array ultrasonic techniques for detection and sizing of defects, together with metallographic replication for monitoring creep damage accumulation and portable hardness testing for monitoring degradation of mechanical strength.
- Type IV creep damage at butt welds in P91 piping tends to be less apparent at the surface of the component until late in life, which may restrict the usefulness of replication. Therefore, we use its unique Scanning Force Microscope (SFM) to detect nanometer-scale creep cavities that appear at the surface earlier in life than the micron size cavities that can be detected by replication.
- Using P91-specific damage assessment guidelines, the remaining creep life of components can be estimated using the on-site observations of creep damage
- AMCO Integrity Pty Ltd can also carry out code-based calculations of creep life using either deterministic or probabilistic methodologies.
Recent Post
Experts Engineers Support
Global Resources
Customer Satisfaction
Miniature Sample Removal
For Quality Checks and Life/Condition Assessment
AMCO Integrity Pty Ltd offers a non-destructive sample removal service using Electric Discharge Sampling Equipment (EDSE). Using the EDSE, thin samples of material (typically 1-5mm thickness) can be removed from the component surface for analysis under laboratory conditions. Mechanical tests can be carried out using miniature specimens, such as small punch or miniature uniaxial creep tests, and thus remaining life assessment can be performed.
Miniature Sample Removal for Quality Checks and Life/Condition Assessment
At-site inspection using replication and hardness testing can identify P91 material or welds with abnormal microstructures and/or unacceptably low (or high) hardness levels, but only at the surface of the component, so the results of these at-site inspections can be affected by decarburization and may not be representative of the bulk of the material.
The EDSE has proven to be a particularly useful tool when verifying the material condition of P91 components in order to resolve material quality issues. Examination of microstructure and hardness changes through the thickness of the EDSE sample can differentiate between a surface effect and an abnormal material condition.
Defect/ Crack Assessment
If cracks are found by NDE, then we can carry out crack growth and remaining life assessment using our partner ‘Crackfit’ defect assessment software. This tool contains a range of crack and component geometries so enables the analysis to be performed rapidly which is crucial when run- repair-replace decisions have to be made.
Our material property database includes crack growth properties for HAZ and weld metal as well as P91 base metal at different temperatures, so the specific properties for the actual crack location can be used, leading to more reliable life estimations.
Root Cause Failure Analysis
AMCO Integrity Pty Ltd carries out the metallurgical investigation and root cause analysis of failures and cracking in P91 components/welds. In the recent past, we have investigated a range of failures of T91 tube components and welds, and cracking in P91 pipe and drain-line components in conventional boilers and HRSGs. In these investigations, we identified the damage mechanism and the root cause of the damage, and thus remedial actions and solutions to the problem have been identified.
Consultancy and Guidelines on Materials and Welding
AMCO Integrity Pty Ltd can provide P91 users with advice and guidance on the metallurgy and welding issues of grade 91 materials, such as reviewing weld procedure specifications (WPS) for similar and dissimilar metal welds, an inspection of NDE records, and guidelines for repair welding of P91.
Get A Free Quote
Other Related Services

Fitness for Service (FFS)

Turbine Materials Evaluation
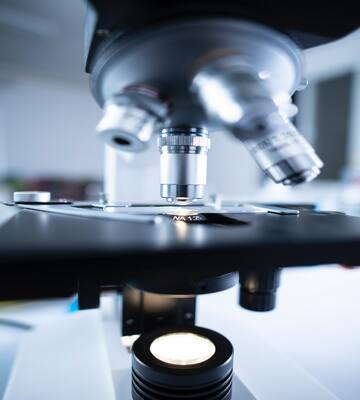
Failure Analysis

Remaining Life Assessment (RLA)

Boiler Inspection/ Assessment
